The 2025 Custom Home: An In-Depth Analysis of Architectural, Technological, and Lifestyle Trends - part 4
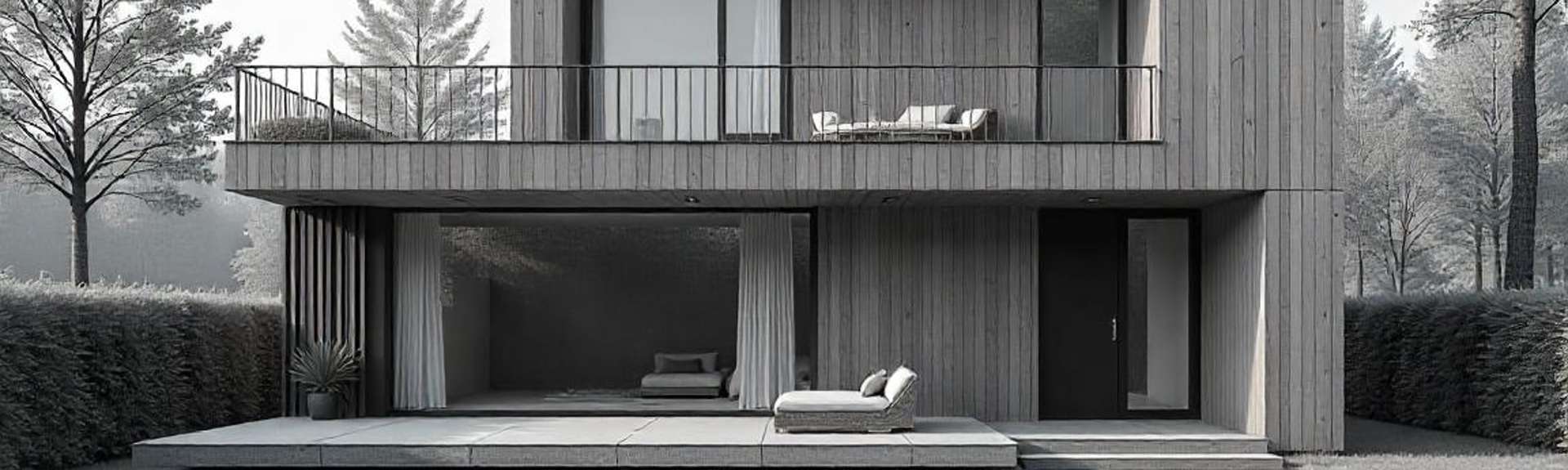
The Technology and Engineering Nexus - High-Performance Systems and Structures
The realization of the 2025 custom home—sustainable, well, and resilient—is made possible by a sophisticated nexus of advanced technology and innovative engineering. High-performance systems are no longer optional upgrades but are integral to the core design, enabling homes to achieve unprecedented levels of energy efficiency and comfort. Simultaneously, new construction methodologies are challenging the dominance of traditional stick-framing, offering compelling alternatives that promise greater speed, sustainability, and structural integrity. This section provides a technical deep dive into the systems and structures that form the backbone of the modern high-performance residence, from a cost-benefit analysis of renewable energy systems to an assessment of emerging framing technologies like mass timber and 3D concrete printing.
The Path to Net-Zero: A Cost-Benefit Analysis of Solar and Geothermal Systems
Achieving ambitious sustainability goals, particularly the standard of a Net-Zero Energy Home, hinges on the integration of advanced energy generation and high-efficiency HVAC systems. The two leading technologies in the custom home sector are solar photovoltaics (PV) for on-site electricity generation and geothermal heat pumps for ultra-efficient heating and cooling. While both require a significant upfront investment, a detailed cost-benefit analysis for 2025 reveals that a combination of technological advancements, government incentives, and long-term energy savings is increasingly making them a sound financial decision, not just an ideological one.
- Solar Photovoltaic (PV) Systems: Solar panels are a cornerstone feature of the modern sustainable home. While the broader residential solar market experienced some headwinds in early 2025 due to high interest rates and policy uncertainty, leading to a slight decline in installation volume, the technology remains a key specification in new custom builds. This is especially true in states with solar mandates for new construction, like California, or in regions with high electricity costs where the ROI is more rapid. A significant trend is the increasing pairing of solar arrays with battery storage systems; in 2024, over 28% of new residential solar capacity was installed with storage, a dramatic increase from under 12% the previous year, reflecting a growing desire for energy resilience and independence. C
- ost & ROI: The average cost of a professionally installed residential solar system in 2025 is approximately $3 per watt, with a typical whole-home system ranging from $25,000 to $45,000 before incentives. The 30% federal Residential Clean Energy Credit remains a powerful driver, significantly reducing this upfront cost. While prices are generally trending downward due to manufacturing improvements, fluctuations in material costs and potential tariffs can impact the final price. The financial return is compelling: payback periods typically range from 6 to 10 years, and multiple studies confirm that homes with an owned solar system command a higher resale value, often selling for 4% to 8% more than comparable non-solar homes.
- Technology: 2025 sees the deployment of more efficient panels, with some models exceeding 25% conversion efficiency. Other innovations gaining traction include bifacial panels that capture reflected light, transparent solar cells that can be integrated into windows, and smart management systems that use AI and IoT to optimize energy production and consumption.
- Geothermal Heating and Cooling Systems: Geothermal heat pumps are considered a "must-have" for many high-end sustainable homes, representing the gold standard in HVAC efficiency. These systems leverage the stable temperature of the earth to heat and cool a home, making them up to 65% more efficient than conventional HVAC systems and reducing energy consumption by 25-50%. A recent survey revealed that while environmental benefits are a factor, the primary drivers for homeowner adoption are long-term cost savings and the exceptional longevity of the equipment.
- Cost & ROI: The primary barrier to adoption is the high upfront cost, which averages between $15,000 and $35,000, or $4,000 to $8,000 per ton of capacity. This cost is significantly influenced by the drilling or excavation required for the ground loops. However, installing a system during new construction is 20-40% less expensive than retrofitting an existing home. Like solar, geothermal systems are eligible for the 30% federal tax credit, which substantially improves the financial equation. Despite the high initial outlay, the combination of the tax credit and dramatic energy savings can result in a payback period of under 10 years, with some case studies showing an ROI in as few as 2 to 8 years. The exceptional durability of the system—with the indoor heat pump lasting over 25 years and the underground loops warrantied for 50 years or more—makes it a robust long-term investment.
- Case Studies: Real-world examples validate the financial benefits. A NYSERDA case study of a single-family home retrofit projected a break-even point of less than 10 years, with the owner highlighting the added benefits of improved indoor air quality (less dry heat) and independence from volatile propane prices. Another case study of a 2,500 sq ft new construction project showed that a geothermal system reduced estimated annual utility bills from over $3,600 to just $960.
The following table provides a comparative analysis of these high-performance systems against traditional HVAC.
Feature |
Geothermal Heat Pump |
Solar PV with Battery Storage |
Advanced Air Source Heat Pump |
High-Efficiency Gas Furnace + AC |
Average Upfront Cost |
$15,000 - $35,000+ |
$25,000 - $45,000+ (system) +$10,000 - $20,000 (battery) 48 |
$8,000 - $20,000 |
$7,000 - $15,000 |
Federal Tax Credit (2025) |
30% |
30% |
Up to $2,000 |
Up to $600 |
Annual Operating Cost |
Very Low ($100-$200/month electricity) |
Near Zero (potential for net metering credits) |
Low (highly efficient electricity use) |
Moderate to High (dependent on gas/electricity prices) |
Projected Energy Savings |
Up to 70% vs. traditional |
Can eliminate electricity bills |
30-50% vs. older systems |
Baseline (95-98% efficiency) |
Typical ROI Payback Period |
2 - 10 years |
6 - 10 years |
5 - 12 years |
N/A |
System Lifespan |
25+ years (pump) 50+ years (ground loop) 55 |
25 - 30 years (panels) 10 - 15 years (battery) |
15 - 20 years |
15 - 20 years |
Key Benefits |
Extremely quiet; no outdoor unit; consistent performance regardless of air temp |
Energy independence; blackout protection; potential to earn credits |
Lower upfront cost than geothermal; no ground excavation required |
Lower upfront cost; mature technology |
Key Considerations |
Requires significant yard space or drilling; high upfront cost |
Dependent on sun exposure; battery adds significant cost; policy uncertainty |
Performance decreases in extreme cold; visible outdoor unit |
Relies on fossil fuels; subject to price volatility; higher carbon footprint |
The Resilient Home: Climate-Adaptive Design and Advanced Water Management
The increasing frequency and intensity of extreme weather events have propelled climate resilience from a niche concern to a critical design parameter for custom homes in 2025. Building a resilient home involves a dual strategy: constructing a durable physical envelope designed to withstand regional climate threats and implementing advanced systems to actively manage vital resources, particularly water.
The demand for climate-resilient features is now mainstream. A recent Zillow study found that an overwhelming 86% of recent homebuyers consider it very important for a home to have at least one such feature. This is translating into tangible market trends, with property listings increasingly highlighting features like flood barriers, seismic retrofitting, and fire-resistant construction. For custom builds, this means specifying materials and methods tailored to the local environment. In wildfire-prone areas of the Mountain West and California, this includes using non-combustible or fire-resistant siding like fiber cement or metal, creating defensible space through landscaping, and utilizing mass timber for its charring properties. In coastal regions like Florida, which are susceptible to hurricanes, design focuses on robust structural systems, impact-resistant windows, and roof designs that can withstand high winds. Alongside building a strong envelope, advanced water management has become a key component of both sustainability and resilience. In an era of increasing droughts and unpredictable rainfall, controlling this resource is paramount. High-end custom homes are now integrating sophisticated rainwater harvesting systems, which capture runoff from roofs and store it in cisterns for landscape irrigation and other non-potable uses, reducing reliance on strained municipal water supplies. Equally important is the management of water inside the home to prevent waste and damage. This is where smart water monitoring technology has become a critical feature. Systems from companies like Moen (Flo) and Phyn (Phyn Plus) use AI-powered sensors installed on the main water line to learn a home's unique consumption patterns. By monitoring water flow and pressure 24/7, these systems can instantly detect anomalies, from a tiny, hidden drip behind a wall to a catastrophic pipe burst. Upon detecting a serious leak, they can send an immediate alert to the homeowner's smartphone and, most critically, automatically shut off the water main to prevent widespread damage. These systems also provide detailed reports on water usage, empowering homeowners to identify areas of high consumption and make informed decisions to conserve water, thus contributing to both resilience and sustainability goals.
The Future of Framing: Case Studies in Mass Timber (CLT) Construction
While traditional light-wood framing remains the standard for most residential construction, mass timber—and particularly Cross-Laminated Timber (CLT)—is rapidly emerging as a compelling and innovative alternative for custom homes in 2025. Driven by a desire for sustainability, faster construction, and a unique biophilic aesthetic, mass timber is transitioning from a niche material used primarily in large-scale commercial projects to a viable option for the single-family residential market. Mass timber products are engineered by layering and bonding smaller wood elements to create large, exceptionally strong structural components like panels, beams, and columns. This approach offers a host of benefits that align perfectly with the core trends of 2025:
- Sustainability: As a renewable resource, wood sequesters carbon for the life of the building. Using mass timber in place of carbon-intensive materials like concrete and steel can dramatically reduce a home's overall carbon footprint, making it a powerful tool for sustainable design.
- Construction Speed and Efficiency: Mass timber components are prefabricated to precise specifications in a factory setting. This allows for rapid assembly on-site, often with a smaller crew, which can shorten construction timelines by 25% or more compared to traditional methods. This efficiency helps mitigate risks associated with weather delays and labor shortages.
- Performance and Resilience: Mass timber is structurally robust and performs exceptionally well in both fire and seismic events. During a fire, the thick panels develop a protective layer of char on the outside, which insulates the interior wood and slows combustion, allowing the structure to maintain its integrity for a significant period. Its combination of strength and light weight also makes it highly resilient in earthquakes.
- Aesthetics: One of the most appealing aspects of mass timber is the ability to leave the wood structure exposed on the interior. This creates a warm, natural, and biophilic environment, reducing the need for additional finish materials like drywall and allowing the structure itself to become the primary aesthetic feature.
Despite these advantages, several challenges currently limit its widespread adoption in single-family homes. The primary hurdle is cost, as mass timber often carries a price premium over conventional framing due to a still-developing U.S. manufacturing base and supply chain. Another significant challenge is the expertise gap; there is a relative shortage of architects, engineers, and builders with deep experience in mass timber design and assembly, especially at the residential scale. Finally, there are technical hurdles, most notably the integration of mechanical, electrical, and plumbing (MEP) systems. Because solid CLT panels offer no interstitial space for running ducts, pipes, and wires, their routing requires meticulous planning and coordination from the earliest design stages. Protecting the wood from water damage during the construction phase is also a critical risk that must be carefully managed. Nonetheless, inspiring case studies are demonstrating the potential of mass timber in custom homes. The "Haus Gables" project in an Atlanta suburb, a 2,200-square-foot home designed by Jennifer Bonner, uses unadorned, painted CLT to create a striking, sculptural form with a warm, minimalist interior. In a more remote setting, the "SoLo" home in British Columbia, designed by Perkins&Will, is a stunning off-grid retreat made almost entirely of Douglas fir. It is certified to the rigorous Passive House standard and showcases how mass timber can be used to create a highly resilient and sustainable luxury residence in a harsh climate. These projects serve as powerful precedents, paving the way for broader adoption as costs decrease and industry expertise grows.
The Printed Frontier: Assessing the Viability of 3D Concrete Printing in Custom Homes
On the cutting edge of construction technology, 3D Concrete Printing (3DCP) is emerging as a potentially revolutionary method for building homes. This innovative process uses a large-scale, gantry-style robot to extrude a specially formulated concrete mix layer by layer, building the walls of a structure from a digital design file. While still in its early stages of adoption, 3DCP is being explored for a wide range of applications, from providing rapid and affordable housing solutions to creating unique, architecturally expressive custom homes. The potential benefits of 3DCP are significant and align with key industry pressures:
- Speed and Cost: The most compelling advantage is the dramatic reduction in construction time. The structural walls of a house can be printed in a matter of hours or days, rather than weeks. This speed, combined with a drastic reduction in on-site labor needs (a 3D printer can be operated by just two or three technicians, replacing a full framing and masonry crew), has the potential to significantly lower overall construction costs.
- Sustainability and Waste Reduction: As an additive manufacturing process, 3DCP is incredibly efficient with materials. The printer deposits concrete only where it is needed, virtually eliminating the waste associated with cutting and fitting materials in traditional construction.
- Design Freedom: The technology liberates architects from the constraints of traditional rectilinear forms. 3D printing makes it possible to create complex, curved, and organic walls and structures with no additional cost or complexity, opening up new avenues for architectural innovation.
- Resilience: The resulting structures are made of concrete, offering inherent durability and resistance to threats like fire, water damage, high winds, and pests.
However, the technology faces several performance challenges and hurdles to widespread adoption:
- Regulatory and Code Compliance: A primary barrier is the lack of established building codes and standards specifically for 3DCP. Projects often must navigate a lengthy and uncertain alternative approval process with local building officials, which can add time and risk.
- Technical and Material Limitations: Current challenges include the physical size limitations of the printers, the need for highly specialized concrete mixes that can flow through the nozzle yet set quickly enough to support subsequent layers, and the ongoing development of methods to effectively integrate structural reinforcement (like rebar) to provide the necessary tensile strength, particularly for seismic performance.
- Long-Term Durability and Performance: While concrete itself is a highly durable material, the long-term performance of a layered, printed structure is still the subject of ongoing study. The integrity of the bond between the printed layers is critical to prevent delamination over time, making the quality of the material mix and the precision of the printing process paramount. If constructed correctly, a 3D-printed home is estimated to have a lifespan of 100 years or more, potentially outlasting conventional construction.
- Systems Integration: As with mass timber, integrating MEP systems, windows, and doors into a solid, printed wall structure presents unique challenges that require new design and construction techniques.
Despite these hurdles, successful case studies are emerging. Projects by the company ICON in Texas have demonstrated the technology's ability to create affordable and aesthetically pleasing homes quickly , while a recently completed villa in Dubai set a Guinness World Record for the largest 3D-printed residence, showcasing the technology's growing scale and capability. These pioneering projects suggest that as the technology matures and the regulatory framework catches up, 3DCP will play an increasingly important role in the future of home building.
The parallel rise of Mass Timber and 3DCP, while materially different, points to a larger, more fundamental shift in the construction industry. Both technologies represent a move away from traditional, on-site, labor-intensive processes toward a future defined by off-site prefabrication and on-site automation. They are two distinct but powerful solutions to the industry's persistent challenges of labor shortages, cost overruns, and construction delays, heralding the most significant structural change in how we build homes in decades.
Attribute |
Mass Timber (CLT) |
3D Concrete Printing (3DCP) |
Traditional Light-Wood Framing |
Construction Method |
Off-site prefabrication, on-site assembly |
On-site robotic extrusion (automation) |
On-site manual construction (stick-built) |
Construction Speed |
High (25%+ faster than traditional) |
Very High (walls printed in hours/days) |
Baseline |
Relative Material Cost |
Premium |
Potential for Savings (less material used) |
Baseline |
On-Site Labor Needs |
Low (smaller assembly crew) |
Very Low (2-3 operators) |
High |
Sustainability Profile |
High (Carbon sequestration, renewable) |
Moderate (minimal waste, but uses cement) |
Moderate (renewable, but higher waste) |
Key Performance Benefit |
Aesthetic, fire/seismic resistance, sustainable |
Design freedom (curves), speed, resilience |
Established, well-understood, flexible |
Primary Challenge |
Cost premium, supply chain, expertise gap |
Lack of building codes, durability questions |
Labor shortages, price volatility, weather delays |